Top 7 Ways to Prevent Equipment Downtime
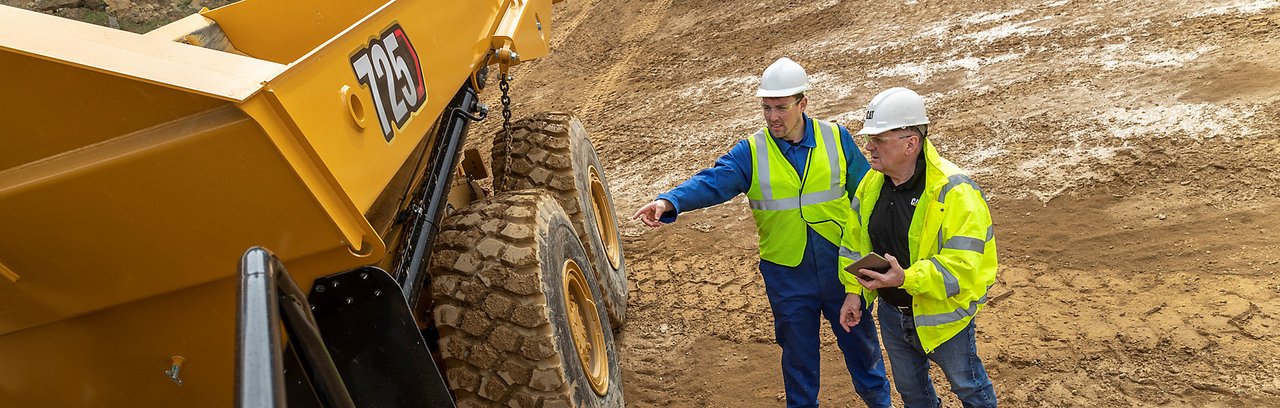
Lost revenue. Costly repairs. Project delays. When a machine is down, it can result in unintended costs that impact your business and reputation.
Learn to prevent downtime before it happens—and identify issues before they turn into bigger problems.
When a machine is down, it can result in unintended costs — from lost revenue to costly repairs. It can also mean project delays that impact your employees, customers and even your reputation.
While you can't always predict machine downtime, you can have a plan to prevent it.
Learn about the causes of equipment downtime and the seven steps you can take to save time, money and keep your crew safe.
1. Preventative Maintenance
Preventive maintenance keeps your equipment running, helping to prevent downtime before it happens. If you skip maintenance, a small problem could result in prolonged downtime.
Start by reviewing your machine's service, parts and maintenance manuals. Your machine's manuals should outline the recommended service intervals for each component and what parts are needed. Be prepared with the supplies and parts you need before the next service is due. Our Cat® Planned Maintenance Kits make it easy by including everything you need in one package.
Avesco Maintenance Agreements - Easy Service and Easy Parts offer flexible service options tailored to your business.
2. Monitor Equipment Performance
Monitoring your machine's performance can help you identify issues before they turn into bigger problems. Operators are often the first to realize something doesn't feel right. If you're not the one behind the controls, take the time to talk with your operators about how each machine if performing. When they do flag an issue, address it as soon as you can.
You can also use software to monitor machine performance for you. Our web-based fleet management tool, VisionLink®, simplifies machine maintenance by tracking the health of your fleet and sending alerts when service is due. You can monitor your machine's hours, how long it’s been since it was last serviced and see a list of fault codes. With this data you can understand what caused a machine to fail and prevent the same issue in the future.
3. Have the Right Equipment and Tools for the Job
Having the right equipment and tools for the job will help prevent downtime and project delays. Before you start a project, evaluate the ground conditions, space constraints and material you're moving to help determine the right equipment.
4. Properly Store Equipment
When you store machines for an extended period, extra care is needed to keep them in good condition. Start by reviewing storage recommendations from the manufacturer. This is often included in the Operation and Maintenance Manual.
Steps to properly store heavy equipment:
- Complete a thorough inspection and all maintenance prior to storing. This should include topping off fuel and hydraulic fluids to proper levels, and slightly over-inflating tires to avoid flattening over time.
- Store your equipment indoors with proper ground protection. A clean, solid base is best. Cover to protect from dirt and moisture.
- Continue regular inspections and maintenance while it's in storage. Start your machine weekly to lubricate the engine and maintain battery power.
5. Monitor the Weather
Weather can cause significant interruptions to projects. Be proactive and have a plan for when bad weather is expected. Check the forecast often, and adjust plans based on timing. You may be able to reschedule a project. Consider operator safety, machine usage and machine storage when determining whether to work in unfavorable conditions. Keeping all of these elements in mind can allow you to stay on schedule while reducing risks.
6. Identify Jobsite Hazards
Unseen hazards at your job site can cause harm to machines and operators, which lead to downtime. Before beginning a project, take a few minutes to check the site for physical and health-related hazards. Check for ground and haul road conditions, clearance and weight limitations, the location of utility lines, the potential for falling or sharp objects, workplace chemicals, and availability of PPE and First Aid.
7. Complete a Machine Walkaround
Machine walkarounds are an essential start and end to each work shift. By performing these daily, you can identify leaks, hose rubs and other problems that can impact a machine's ability to work. Complete this pre- and post-shift and report any maintenance or safety concerns you find to help prevent equipment downtime.
For more information please contact US:
Estonia +372 679 9260 | info.ee@avesco-cat.com | Latvia +371 2 570 17 11 | info.lv@avesco-cat.com | Lithuania +370 52 603 242 | info.lt@avesco-cat.com |